4 Safety Measures to Protect your Workers from Toxic Chemicals


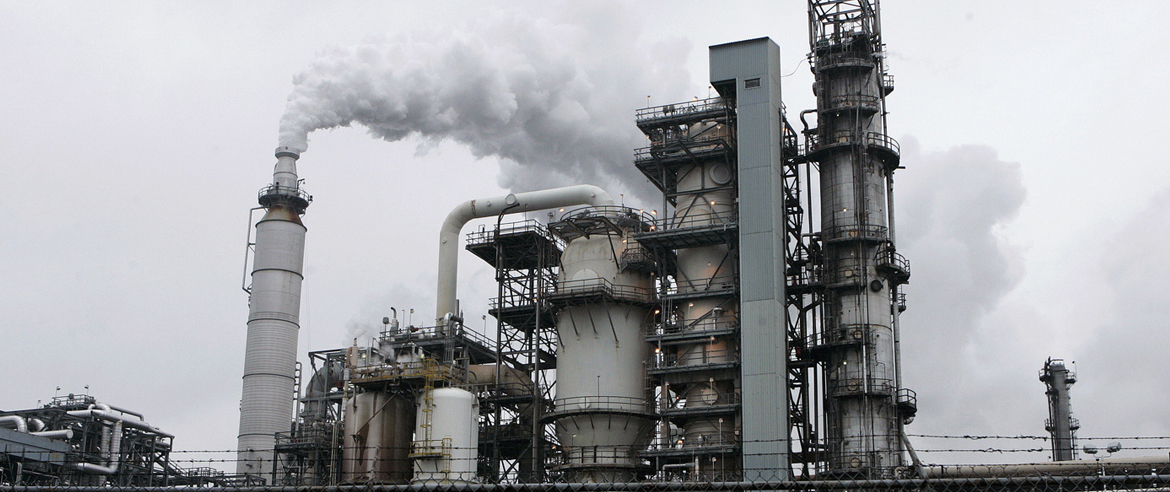
Do your workers know how to handle potential toxic health hazards? Let’s admit that our workers are daily exposed to various health risks which are detrimental to their health, and in many cases, can even lead to their death.
It is thus important for you to keep your plant safe and toxic-free. Here are a few safety measures that you should adopt right away to ensure the well-being of your workers. Check out!
1) Know the exposure limit
In order to protect your workers from any toxic chemicals, it is important for you to know about the Occupational Exposure Limit (OEL). It is the amount of exposure to a certain substance or dust that your workers can handle before it turns out to be a health risk for them.
It is highly recommended to educate the workers on the substances they are dealing with every day. This can be easily achieved by providing related handbooks and Material safety Datasheets (MSDS). This would help them in handling the chemicals and would also make them aware of the risks associated with the harmful toxins which they daily deal with.
Before sending your workers to plant, you should make sure to equip them with Person Protective Equipment (PPE). They should also be taught to wear the protective equipment properly. This would help them in being contaminant-free so that their homes are not infected.
You might also try substituting the existing toxic materials with less hazardous ones. While doing this, ensure that the substitute used has no or less potential risks attached.
2) Use of airlocks
Airlocks help in keeping the air fresh thus protecting your workers from any potential health hazards. There are two types of airlocks that can be used in the plant to ensure the safety of the workers – airtight valves which act as an enclosure in the machinery and the rotary airlock valves which keep the substances flowing through the machinery and the airflow is sealed from the inlet to the outlet flanges.
Although the valves are given the name ‘airlock’, they still tend to leak sometimes. This can be corrected by customizing the valve as per the needs. Further, try to restrict the number of workers entering the plant area to avoid exposure and eliminate health risks.
It is also highly recommended to properly ventilate the plant area so that are at reduced risk of contamination. You may build Local Exhaust Ventilation (LEV) near the leak points to promote fresh air into the enclosed area.
It is also possible to create a barrier between the hazard and the workers using electrical insulation, machine guards, and remote control.
3) Clean surroundings
It is already discussed that workers must be given MSDS to complete. This makes them aware that the cleaning products must not be mixed with chemicals. While cleaning the surfaces, wet wipes can be used instead of dry ones. This is done so as to prevent dust from moving up and mixing with the air resulting in danger. It is also important to build sanitary features into the machinery.
The method of building U-shaped motor pockets into the valves can be adopted for extra safety. If the bottom of the valve is V-shaped, there is a tendency for materials to get accumulated. But, U-shaped pockets enable more flow and make cleaning easier. The build-up of materials can also be prevented by using inboard bearings and glandless shaft seals.
As an additional step, follow proper labeling standards and keep the desired materials in properly labeled containers. In the case of any mismatch, instruct your employees to inform supervisor immediately.
4) Avoid using corrosive materials
A corrosive material is highly reactive and is hazardous. When it comes in contact with other substances, it can lead to great damage. It is thus highly recommended to use materials like stainless steel to prevent the risks of corrosion or other chemical reactions that could take place inside the valves while fixing rotary airlock valves or ball valves.
Educate your workers to not eat or drink anything while handling toxic materials to avoid any contamination.
Your Turn
Contamination inside the plant area can lead to various potential health hazards including the likes of skin irritations, sensitization and even dangerous diseases like cancer in some cases. According to estimates, millions of workers are exposed to harmful chemicals daily. Thus, it becomes imperative to educate your workers in order to prevent any mishaps from happening.
Ignorance has caused more destruction in the past than anything else. In most cases, the problem is caused by unexpected releases of flammable, reactive liquids during various processes conducted in the plants. Helping the workers to use the protective accessories and advising them to stay away from chemicals whenever possible can avoid a lot of accidents.
Further, care should be taken to train your workers regarding emergency equipment and procedures including emergency reporting, evacuation, dealing with fires and others.
Having proper safety installations near your plant would not only reduce the risks but also make sure that your workers are healthy throughout with no causalities, which would ultimately boost your production.