3 Preventive Measures For Maintaining The Industry Valves Rightly


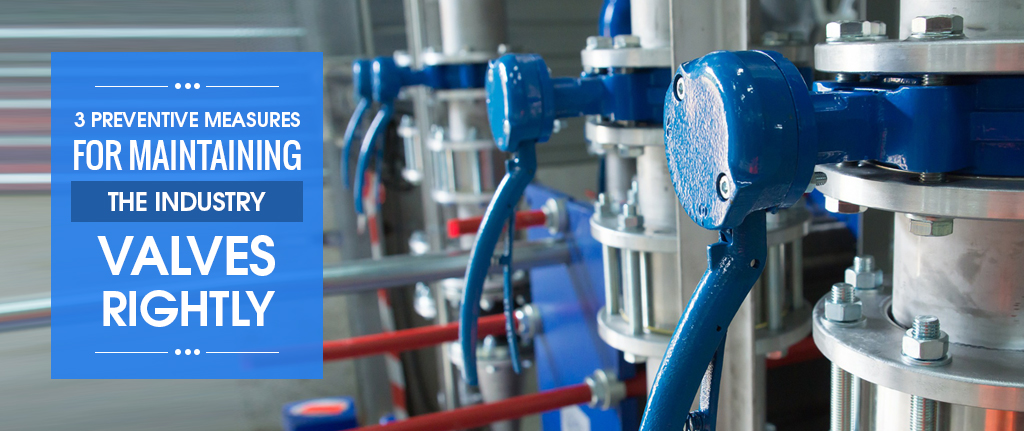
Have a damaged valve and looking for proper preventive measures to maintain it going forward? Well, we just got you covered!
An industry valve finds a range of uses in various daily applications and processes, and therefore, checking the valve for any discrepancy is essential to avoid hazards. Valves form a vital part of a piping set up that carries liquids, vapors, and gases. Today, there is an array of valves available with us including the likes of the plug, gate, butterfly, diaphragm, control valves or pressure relief to name a few. Certain valves are automatically operated while others need to be a manually operated or need to be the actuator or hydraulic operated.
Checking of defective valves is necessary to avoid any hazards and system failure. In piping arrangements, industrial valves have a deciding role in managing fluids. The different valves handle applications such as on-off, flow diversions or throttling. Failure of any of these valves is not only critical to the system but for employees to who might be working in the plant.
This is the reason perhaps why preventive maintenance of valves is necessary to fight against downtime and high replacement costs. With that being said, let’s have a quick look at 3 preventive measures that should be kept in mind for proper preventive valve maintenance:/p>
1) Scheduled Shutdown Maintenance
Annual maintenance should be a significant part of every plant or facility. The all-round quality of the product of a plant revolves around its machines’ performance and systems. It becomes vital to guarantee that all equipments and their parts are performing in peak condition to produce quality results.
Scheduled shutdown maintenance is necessary to be prepared beforehand regarding faulty parts which might need replacement. However, sticking to a compact plan can minimize any sudden disruptions and make the process work smoothly. Here are a few steps that should be taken care of:
- Groundwork
A major chunk of the work on annual maintenance should be performed even prior to fixing a date. This involves compiling historical details for every part of the equipment, formulation of a list of the things to be maintained and the time required.
Actually, all major operational areas are included during yearly maintenance. In this light, some portions of the plant, rather than the complete plant should be shut down, relatively for a given time period. In fact, scheduled maintenance requires documentation plus data storage for the purpose of archiving, fixing every electrical connection, inspecting and also lubricating any part that needs it.
You also require inspection regarding condensation plus water damage along with supervision of each and every hose or pipe for leakage. Moreover, the entire filters, pulleys as well as the belts require inspection for any wear or tear.
- Operational Testing
Next step is to conduct a thorough operational testing which is vital for ensuring that all the parts are functioning at peak levels to assure excellent quality of the final product in a plant. Certify that every control system is operating properly and look into any excess noise or tremor to avoid problems.
2) Routine Inspections
In addition to annual checks, valves should be inspected and examined on a regular basis. The control valve regulates flowing liquids like steam, gas, water and chemical compounds and is the general final control component. Such valves automatically control the pressure or flow rate and handle plant’s functioning at various pressures and temperatures. It is thus highly recommended to conduct a special monitoring of all control valves that operate under high temperature and pressure.
The shut-off valves form another important part and are air operated. During emergencies, shut off valves help in avoiding disaster by detecting any leaked gas or chemical. When closed, these valves provide a cent per cent closure and when in open state, they give a cent per cent full bore. Here are a few steps that should be adopted on a regular basis for thorough inspection of the valves:
- You should tighten the bolts and nuts properly. Open and close the valves to see that they do not get seized.
- Valve leakage can be detected through the mineral deposit or corrosion and rusting on the casing. Likewise, you should test static valves for determining an exact reading given by the valve position indicator.
- Examine everything in the plant system for defects like brittleness and cracks and anything that might create leakages.
- Perform alarm tests to find out if they are working fine by buzzing at the slightest emission of hazardous substances.
- Inspect systems comprehensively and make it safe for your co-workers and users
- Look at valves closely to make a better inspection. See the way the valves bend and check their alignment. Check out for bents or warped stems within the valves as they have a bearing on the working of the valves.
- Valves that manage compressed air, gasses or refrigerants can be examined with a plain soap and water mix. You can spray this combination and look out for the formation of bubbles. Another method is by applying an electronic leak detector which can detect small leaks and marginalize the dangers of error.
Leakage detection in various parts of the industrial valves is integral as they might lead to revenue loss and in rare cases, can even cause loss of lives.
3) Clean
Once all the inspections are done, cleanliness is the next essential step. Cleaning is essential to boost the life of your valves. It is highly recommended to employ thin oil coats upon the rods and adjust the excess loose or tight linkages.
To tidy the valve casing, towel, as well as wire brush, can be used. Valves in dusty facilities or the ones that deal with corrosive agents should be cleaned every 6 months or more based on the seriousness of the problem.
Over to You
Adopt the above-mentioned steps and boost the life of your plant by having proper preventive maintenance of valves. Above all, have a sound knowledge about the working of every valve type as that will assist you in designing a valve maintenance plan accordingly.
What are your views on this? How do you ensure that your valves are functioning properly? For more information about various valves specifically required for your industrial plants / business, Contact Flowspec and we will be happy to answer your questions and give you all the details you need.