Characteristics and applications of ball valves


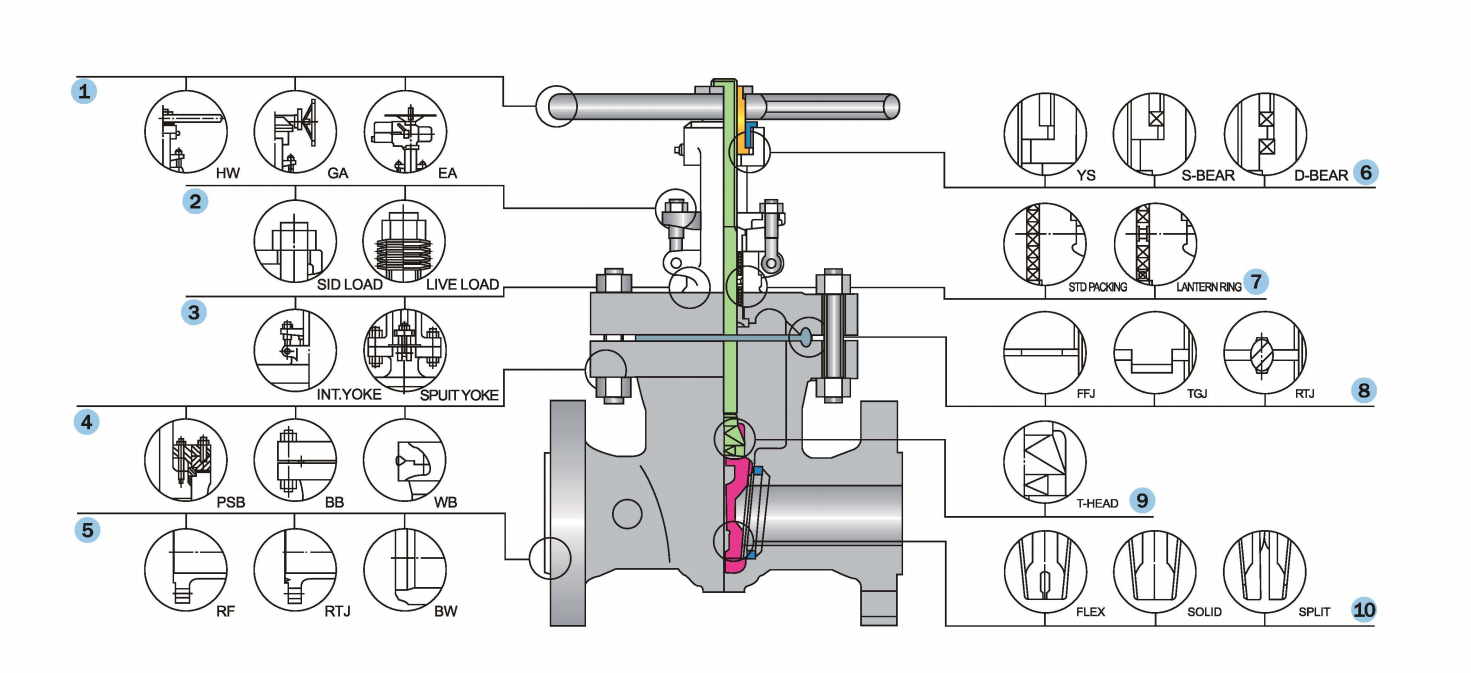
Ball valves evolved from plug valves and, similarly, achieve opening and closing through a 90-degree rotation. They can be tightly closed with only a small rotation and minimal torque. The fully streamlined inner cavity of the valve provides a straight flow path with extremely low resistance for the medium.
Ball valves are characterized by their compact structure, ease of operation and maintenance. They are suitable not only for general working media such as water, solvents, acids, and natural gas, but also for media under harsh working conditions, including oxygen, hydrogen peroxide, methane, and ethylene. The valve body can be either integral or combined.
As a new type of valve widely adopted in recent years, the closing part of a ball valve is a sphere, which rotates around the center line of the valve body to open or close. In pipelines, it is mainly used to cut off, distribute, and change the flow direction of media. Its advantages are as follows:
The lowest flow resistance (virtually zero);
Not prone to jamming during operation (even without lubricant), making it suitable for corrosive media and low-boiling-point liquids;
Capable of achieving complete sealing within a wide range of pressure and temperature;
Fast opening and closing, with some structures taking only 0.05-0.1 seconds, suitable for automated systems of test benches, and the operation is impact-free;
The spherical closing part can automatically position itself at the boundary positions;
When fully open or fully closed, the sealing surfaces of the sphere and valve seat are isolated from the medium, preventing erosion by high-speed media;
Compact in structure and lightweight, making it an ideal choice for low-temperature medium systems;
The valve body is symmetrical (especially the welded valve body), which can well withstand pressure from the pipeline;
The closing part can withstand high pressure differentials when closed;
Fully welded ball valves can be directly buried underground, protecting internal components from corrosion, with a maximum service life of 30 years, making them ideal for oil and natural gas pipelines.